World’s most neglected barcode printer
World’s most neglected barcode printer
I promised Sue I wouldn’t mention her company name when I wrote this, but I want to show you how neglected a barcode printer can be and still work. Here are the consequences if you don’t get your barcode printer serviced, keep it clean or look after it!

I went to visit Sue and see how her printer is performing and couldn’t resist taking this photo.
This is a pretty powerful endorsement of just how durable Zebra printers are.
This Zebra S4M is seven years old and never been serviced (and I think it’s probably never been cleaned). It’s been printing several thousand labels a week, without a problem.
You can see it is coated in a layer of dust inside and out and the printhead was thick with black label and ribbon residue. The platen roller (if you don’t know what a platen roller is – there’s a picture below) was also cut (never use a knife to get labels out of your printer).
Three reasons why you need a regular barcode printer service
- It will cost you more to replace the thermal printhead and platen roller. Both will eventually wear out, but they can last twice as long if they’re looked after properly.
- Your once beautiful barcode label printer will produce labels that won’t scan if you don’t service your printer. Labels that can’t be read are a problem because your customers will get angry when they can’t scan them at the checkout.*
- It’s very stressful. Your barcode printer will stop working at the worst possible time – just when you need to print 10,000 labels. You’ll be highly stressed telling your customer that their shipment can’t go out because you can’t print any labels. You’ll be on the phone asking for an engineer to come out to fix your label printer right away and you won’t be having a good day. A same day visit (if you can get one) will cost lots of money.
How to Avoid the Cost and Stress of Neglected Label Printers
If it’s been a while since you had your barcode printer serviced or even cleaned – you have a couple of choices – the dependable and the inexpensive options.
Dependable: book an engineer to come out and give your barcode label printer a service. They will clean and check it and replace any parts that are worn or damaged. See more here.

Inexpensive: buy some alcohol cleaning wipes (we sell COSHH compliant packs of pre-saturated alcohol cleaning wipes in sealed packets) and get the vacuum cleaner to work.
Vacuum your printer out and clean the printhead and platen roller with the wipes.
Print a test label and check it for quality – there shouldn’t be any white lines appearing in solid blocks of print. If there are – it indicates your printhead is wearing out.
Take a close look at the platen roller and check it for cuts or wear. There’s a picture of a platen roller below. Contact us if you need any help and we’d be happy to advise. To find out more about our printer support options see our printer support page here. We have an easy to use guide to cleaning your barcode label printer – see it here.
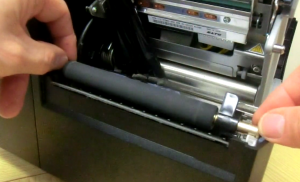
*You probably won’t even realise your labels are unreadable until you have ten thousand products in the shops all with bars missing from the barcodes. Perhaps buying an entry level barcode scanner to test scan every day might be a worthwhile investment?