All posts by Miles
How to Print Labels with NiceLabel
Validate your Labelling System
Training your staff to use the thermal label printer
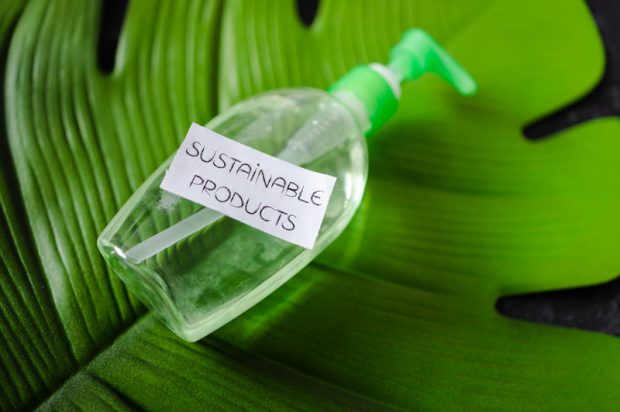
Corporate Environmental Responsibility (CER) and Labels
Labels for your products
What Do You Want Your Product Labels To Say?
Step 1: Request A FREE Quote
We Help You Choose the Right Labels For Your Products.
About
Expert labels are specialists in producing beautiful labels to make your products stand out from crowded shelves. From low cost paper labels to clear, waterproof labels – we help you sell more.
We have more than twenty years experience making sure your labels are delivered on time to do the job they’re supposed to do, every time.
Start by getting a free no obligation quote by clicking here.
Products:
Batch & Serial No. Labels
Print your own, or let us print your batch and serial numbers for you. Choose numbers, 1D or 2D (QR Codes) Barcodes.
Tamper and Security Labels
Specially cut tamper-proof security labels or high security holograms to protect your products.
Waterproof Labels
Choose from a wide range of materials – printed onto clear or full colour labels .
Let’s talk technical
We supply labels on rolls, either pre-printed or for overprinting with thermal label printers. We make labels to a huge range of specifications – from waterproof, gold or silver foil, clear labels, perforated labels, large rolls and small rolls. We have over 6,000 label dies to cut your labels to the exact size you need. Our labels are made from paper, HDPE, PE, Polyester, Vinyl, PP, Tyvek or any number of specialist materials. We can fully customise your labels with sequential numbering, printing from a database or unique full colour labels.
Expert Labels
- Have been supplying labels, tags, tickets, barcode scanners and printers since 1994
- Use specialist digital printing equipment for full colour label printing
- Are trusted by many of Europe’s best known companies to delivery on time and to exacting standards of quality
- Stand by our products with a money back guarantee
We work with organisations who need high quality labels delivered on time and also value a supplier who provides end-to-end printing and scanning expertise.
Some of Our Clients
Some of the hundreds of clients who trust us for their labels, printers and scanners.
Label Jargon
In the world of labelling and printing, there are lots of phrases we use on a regular basis that may not be familiar to you, our visitor. Here’s your guide to the labelling jargon you’re likely to hear.
Even clients of ours who are well-versed in the lingo sometimes surprise us by wanting to know exactly what we mean by particular terms we might simply take for granted.
So we thought it’s about time someone came up with a handy “jargon buster” to explain what it is we actually mean by some of the labelling jargon you’ll find in our industry.
Proof | A common term that means a prototype version of a label (usually just an electronic image file) that is developed in order to be checked by the customer for accuracy. Once the proof version is approved, the label is ready for production. The last thing you or I want is a spelling mistake on 100,000 labels and proofs are our way to prevent it. |
Face Stock |
|
A layer of paper, film or other material that makes up the “front facing” part of the label. It will usually have a layer of adhesive or glue on the backing, with the viewable words and imagery printed onto the Face Stock. | |
Plates | Usually made of plastic – though sometimes made of other materials such as rubber or metal – plates are used to transfer the ink to the label being printed. |
Applicator |
![]() |
A machine that applies pressure sensitive labels onto an item that is being labelled. (Pressure sensitive labels being the type that stick to the item when you press them onto the item). Often this is a machine that automatically applies the labels – sometimes it refers to a handheld device that is used for labelling. | |
Kraft Backing | Krafting is the process of converting wood into wood pulp. This material can then be made into kraft paper, which is stronger and more durable than ordinary paper. It can be used for Kraft backing paper – often used in the process of picture framing. Not often used with label printers as Kraft paper is thick and doesn’t work well with the sensors that printers use to sense the cap between labels. |
Removable Adhesive | A type of adhesive (“glue”) that allows the label to be removed from the item without leaving much residue behind. This is important for labelling high gloss items such as glass or giftware. For example, the type of adhesive used on sticky writing (post it) notes would be a removal adhesive. |
Peelable Adhesive | This is essentially another term for “removable adhesive”. It refers to the type of adhesive (“glue”) that allows you to peel off a label from its backing as well as allowing the label to be peeled from the item it is eventually stuck on to. |
Permanent Adhesive | An adhesive (“glue”) that binds much more strongly to the item it comes into contact with. Permanent adhesive is very difficult to remove from the item without the use of considerable force. Permanent Adhesive is the most common glue found on labels. |
High Tack | Tackiness refers to the “stickiness” of the adhesive used on the label. A label with high tack will have a stronger adhesive and thus a high degree of “stick”. |
DPI |
|
Standing for Dots Per Inch, this is a well-known measure of the level of resolution for printing this isn’t specifically labelling jargon, you’ll find it in printers and software. DPI literally relating to the number of “dots of ink” that can fit along a printed line that is an inch long. (The equivalent for a computer screen would be Pixels Per Inch (PPI) – though many people use DPI to mean the same thing). Thermal label printers tend to print at 203 dpi – or 8 dots per millimeter. | |
Label Gap | When you have a group of labels attached to a backing sheet (for example a roll of labels), the label gap is the distance between two labels. This is usually around 3mm if labels are used with thermal printers. |
Black Mark |
|
A Black Mark may be printed on the back of the label liner to guide certain types of printer as to where to print the label content. Black marks are essential where a label printer is printing to a clear label. Label printers use a sensor that beams a light through the relatively transparent backing paper and recognises when there is an opaque label. With a transparent label the printer needs another way to recognise the label gap. | |
Across the Web |
|
This refers to the number of labels across the backing sheet. If you’re using a wide printer you can print more labels at the same time and increase productivity. | |
Cores |
|
Tubes which the label sheets are wound around for shipping purposes. Usually made of card or plastic. They come in a range of diameters, 25mm, 44mm or 76mm, along with a range of widths. | |
Tamper Evident |
|
These are labels that display evidence of any lifting or removal from the item they are attached to. They may be used for the purpose of eg preventing price labels being switched onto a different item, or for sealing boxes, computers – even doors shut – with any attempt to open the door displaying evidence of tampering on the label. See the security labels we supply here: http://expertlabels.co.uk/applications/security-labels/ | |
Ultra Destruct |
|
A type of tamper evident label that breaks up like an egg shell if tampered with – thus acting as an obvious deterrent to removal as it will be obviously there has been an attempt to remove the label. This type of label is demanded by the Falsified Medicines Directive. | |
Direct Thermal | This is talking about a type of label or tag printer. A Direct Thermal Label Printer has a print head comprising of thousands of tiny pixels. The pixels on the printhead can be independently heated. Now if you pass a heat sensitive paper or tag material underneath a hot object it will turn black. So if you take a heat sensitive paper and a printhead that can turn on thousands of different little dots, you have a way of printing! This is direct thermal – as opposed to Thermal Transfer printing. Shortcoming of direct thermal printing – is that it only works with specially coated paper or card. The labels or tags printed will turn black if subjected to heat from the sun or elsewhere. |
Thermal Transfer Printing |
![]() If you take a direct thermal printer and place a sheet of ink that melts between the print head and the label or tag you are able to melt the ink onto the label. Thermal Transfer paper have a roll of ink that melts onto the paper using a thermal printhead. |
Printhead |
![]() This is the part of a thermal printer that heats up and melts ink onto the label or tag. Can also heat paper coated with a heat sensitive ink that turns black when heated. |
Useful links
When it comes to barcode specific jargon, GS1, the international barcoding organisation, has a handy glossary explaining much of the barcoding, not necessarily labelling jargon:
GS1 Barcode glossary: http://xchange.gs1.org/sites/glossary/en-gb
How to decide a label budget

How to assess your labels for quality
Substandard labels cost you money, reputation and a great deal of inconvenience. To avoid this, you need a process in place to assess your labels for quality. This is critical in pharmaceuticals and other high compliance industries. If you supply the major retailers you will be fined if your labels are not compliant.
- Barcode and label standards to follow
- How to assess your label quality
- Checking what’s printed on your labels
- Pros and cons of using a basic barcode scanner to assess label barcodes
- Why you would use a barcode verifier to assess labels
- The best way to assess label print quality
- Summary
Read on…
Barcode and Label Standards
For many industries, labels are a critical element in compliance.
Compliance comes in two forms – the label components (size, material, compliance icons, colours, barcodes and required text) and machine readability (ability to scan barcodes).
Industry label standards. Different industries will require different label layouts and will specify icons and certain barcodes, containing certain data. Standards are set by organisations like ODETTE for the automotive sector, FDA regulations for healthcare or EU directives. The scope of different industry label standards is too wide to cover in this article. It is your responsibility to research what your industry label standards are.
Barcode standards. Barcode standards (for example size and shape, bar width, colours or colour contrast) are set by an international organisation called GS1.
GS1 is a not-for-profit organisation that issues barcode numbers and coordinates the way barcodes are developed and used in commerce. It’s an international body that has national offices to provide local help and service.
There are generally two different barcodes used for items at a retail point of sale – GTIN8 and GTIN13. Both these barcodes have clearly defined standards in terms of size, height and width proportions, white space, colours and contrast and bar widths.
For what are known as traded items, i.e. a box of 12 cereal boxes or a pallet of dishwasher powder, the choice of barcodes extends to ITF14, GS1-128 or GTIN8 and 13.
For further details on what barcode to use where, when and how – use this great resource from GS1 – Getting it right – guide to barcoding. It’s a 58 page pdf and helps with all aspects of barcode printing onto packaging.
Once you have taken advice from your industry body, you can finalise the layout and design and check they are compliant.
What needs to be in place is a ‘sign off’ to certify the label has been designed correctly.
In the case of pharamaceutical labels or other high compliance labels, label design software like the Enterprise Edition of BarTender can be configured to prevent labels being printed unless they have been approved by an authorised person.
Once the layout is approved it’s a matter of ensuring labels are printed correctly and consistently to that standard.
How to Assess Your Label Quality
Production faults with labels show themselves with:

- Print not staying on the label or fading and becoming unreadable,
- Adhesives not working – and labels falling off items,
- Adhesives working too well – and labels not peeling off,
- Labels you can’t print onto
- Specific failures such as Peel & Reveal labels failing to ‘reveal’ or failing to shut.
- Varnishes that are patchy
Faults are usually obvious once the labels are used. If your labels are critical then it is important to test the labels before use. QA will need to assess each consignment. Label faults are very rare. Out of thousands of orders a year we get no more than a couple of faults.
Sometimes label faults might be an inconvenience rather than a failure. Try to include label performance in your process evaluations.
If labels are making your processes less than optimal, contact us for help making your labels perform better.
Checking What’s Printed on Your Labels
Variable Label Data
If a label has been designed correctly, the chance of incorrect data being printed on your label or encoded in the RFID chip or barcode is almost nil.
After a label design, layout and data-content is approved the only other point of failure is the origin of the data.
If faulty data is added to your organisation’s database, then faulty data will be printed. Examples of this might be an uncapitalised name on a shipping label. Another example might the wrong post code.
Another thing to look out for are changes upstream in the database. A change to a field in a database might show up as incorrect data printed on a label.
Assessing machine readable labels
Machine readable labels, such as barcoded labels or labels with RFID chips embedded in them, need to be assessed first on what data they contain and then secondly – on how well the label meets the barcode or RFID chip’s technical specifications.
1. Scan barcodes with a barcode reader.
This is the simplest, cheapest and least reliable way to check barcodes on your labels. Contact us for a simple barcode scanner (costs around £100) .
Here’s the approach – it’s really simple – have a routine where you scan codes at the beginning, end of your print run and as many times inbetween as you can. If you can’t read your barcode then investigate the problem and re-print if needed.
This will pick up faults like a printhead failure but it won’t notice much else.
The scope of the barcode quality report is Read or Not Read. Not particularly enlightening.
By scanning a sample of codes it won’t notice irregular problems such as where ribbons have wrinkled on a few labels in a large batch of labels.
Barcode scanners vary in quality and performance – so your scanner might read a code, your customer’s might not. Remember also, your barcodes might be scanned by multiple scanners throughout the supply chain.
Certainly using a phone is not reccomended. Cameras can read badly damaged barcodes much better than barcode scanners.
It’s not perfect but it’s a low cost way to check your labels.
This is not a solution in a regulated industry such as pharmaceuticals or healthcare products, where labels need to be perfect.
2. Using a Barcode Verifier to assess your labels
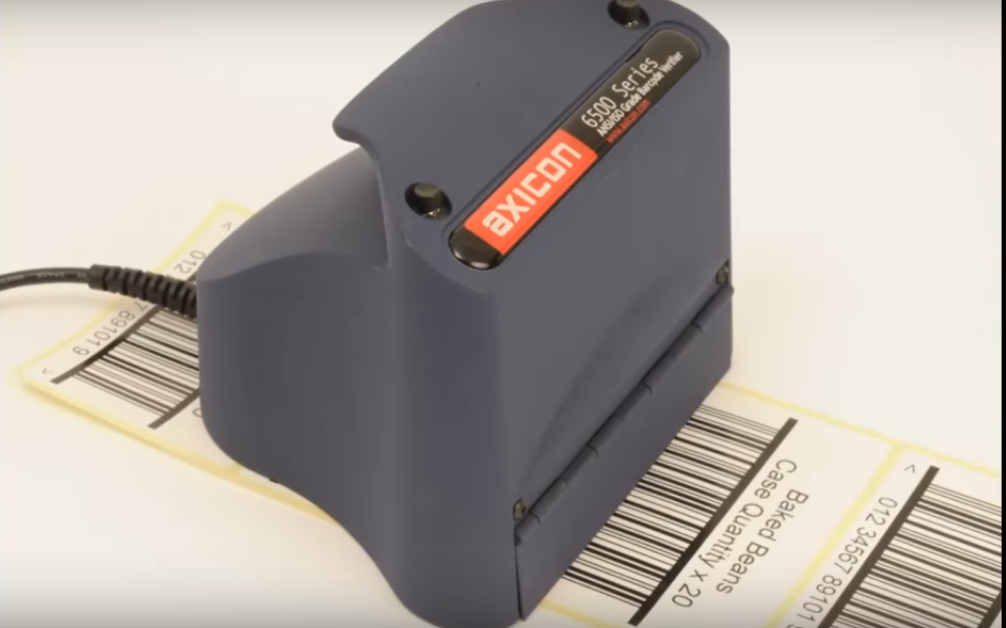
Our previous suggestion was to scan with any old barcode reader and see if it can read. A much more reliable (and one you could argue in court with) is to use an instrument called a barcode verifier.
A Barcode Verifier is a precision instrument that scans and analyses the barcode, taking into account print quality and barcode layout and composition.
A barcode verifier is built to assess against the ISO barcode standards – ISO15416 for linear barcodes and ISO15415 for 2D symbols.
By scanning your barcode you will see if the barcode meets standards and importantly, if it doesn’t, you’ll know what needs to be fixed.
Perhaps more importantly though, you have a record of compliance that you can use in the event of a dispute.
3. Vision Based Inline-Verification for Printed Label Inspection

The best way to check the quality of barcodes and labels in general is to use a camera-based inline barcode verifier. In-line Verifier means that the camera is fitted onto the label printer and checks the print content and quality of every label printed. This label inspection system is (in our opinion) the best way to ensure the quality of labels.
An inline verifier is the only way a printing fault like this one (below) would be noticed, unless you employ someone to watch every label printed.

Vision based label validation – takes an image of every label passing out of the front of the printer. It compares the image to what is meant to be printed and stops the printer if it encounters a problem.
- Vision label quality assurance systems check the readability of 1D and 2D barcodes, along with checking they meet GS1 and ISO standards.
- You can set up thresholds for blemishes – so only significant marks stop the printer.
- Identify incorrect text, i.e. if the wrong data is included in the label.
- Doesn’t slow down the printing process. The printers perform at their usual speed.
- Uses Optical Character Recognition (OCR) to read the text of the label.
- Works with the popular printer manufacturers such as Sato, Printronix, Zebra and Honeywell, though it is only compatible with the high-performance printers in the respective ranges.
- Keeps an audit trail of results.
Sophisticated in-line verifiers can even take data from a spreadsheet or database and ensure labels include data from the database.
Set up is reasonably simple: print a label and have it pass through the verifier.
Using the configuration setting – select areas of the label that will change and tell the software what should appear there. Set up areas of the label that need to be ignored.
Let it print.
The printer can be fitted with a light tower that shows a red light if the system encounters an error and needs to stop.
A complete vision based label verification systems cost between £20,000 and £25,000 depending on the thermal printer and any additional training or system validations.
Summary
- Contact your industry body and find out what the labelling standards are.
- Talk to us about getting your labels designed to meet your industry standard. That might mean using label design software (if you’re going to print labels yourself) or engaging a graphic designer.
- Sign off your final label design.
- Check your labels for quality (such as stickiness or colour) before you need to use them. Ideally when you receive them.
- Have a system in place for reporting faulty labels.
- If you’re printing your own labels, check the labels (including barcodes) contain the correct information – and that the barcodes/RFID chips read correctly at the start and end of each print run.
- If the consequences of faulty labels are serious, invest in a barcode verifier to assess barcode quality.
- If the process of assessing labels is too time consuming and costly, invest in a camera based label quality assessment tool that will check every label printed.
Contact the experts for labelling advice.
Useful Links
GS1UK.org – the UK branch of the international barcode standards organisation, GS1.
‘Getting it Right – Guide to Barcoding’ pdf from GS1.
Updated 7 Mar 2021.